Introduction
Chain hoists are indispensable in countless industries—from manufacturing to construction, oil and gas, mining, and even maritime operations. While their standard design serves well in controlled environments, hazardous and extreme environments demand more than just strength and lifting capacity. Whether used underwater, in explosive atmospheres, or near high-radiation sources, traditional chain hoists face significant performance, safety, and durability challenges.
To operate reliably in such conditions, chain hoists must undergo specialized design adaptations. These adaptations focus on corrosion resistance, temperature tolerance, explosion-proofing, and remote operation capabilities. This article explores how chain hoists can be engineered or redesigned to function safely and efficiently in extreme and hazardous environments, supported by examples, innovations, and material science advancements.
1. Understanding Extreme and Hazardous Environments
Before delving into specific design solutions, it’s important to define what constitutes an extreme or hazardous environment for lifting equipment:
a. Underwater/Marine Environments
-
High humidity and full immersion in saltwater
-
Corrosive conditions causing rapid metal degradation
-
Pressure differentials depending on depth
b. Explosive or Flammable Zones (ATEX/IECEx Classifications)
-
Presence of volatile gases, vapors, or combustible dust
-
High risk of ignition from electrical sparks or static charge
c. High-Radiation Areas
-
Nuclear facilities or radioactive material handling zones
-
Rapid deterioration of materials due to radiation exposure
d. High-Temperature or Cryogenic Zones
-
Foundries, refineries, or cold storage logistics
-
Risks of material expansion, brittleness, or malfunction
2. General Design Limitations of Standard Chain Hoists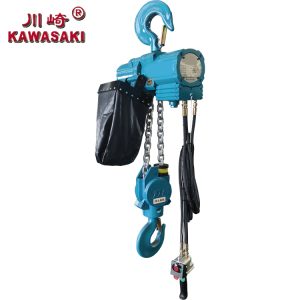
Standard industrial chain hoists—whether manual or electric—are not inherently suited for these harsh conditions. Common vulnerabilities include:
-
Steel corrosion from moisture or salt
-
Electrical sparking from motors or control units
-
Lubricant breakdown under extreme temperatures
-
Material fatigue due to radiation or thermal stress
Redesigning hoists for harsh environments requires addressing these shortcomings through materials, sealing, power systems, and safety technologies.
3. Key Engineering Adaptations by Environment
A. Underwater and Marine Applications
i. Material Selection
-
Use of marine-grade stainless steel (AISI 316) for housing, hooks, and chains
-
Bronze or brass bushings to avoid corrosion and galvanic reactions
-
Coatings: Epoxy, Teflon, or zinc-rich primers provide extra corrosion resistance
ii. Sealing and Waterproofing
-
Use of IP68-rated enclosures for motors and electronics
-
Double O-ring sealed bearings and chain drives to keep out water
-
Drain valves and pressure compensation systems to balance internal and external pressure
iii. Lubrication
-
Marine-grade greases that resist water washout and stay effective underwater
-
Grease lines that allow remote reapplication without dismantling the unit
iv. Remote Operation
-
Tethered or wireless control systems allow divers or ROVs (remotely operated vehicles) to operate hoists from a distance
-
Hydraulic or pneumatic power preferred over electric in fully submerged conditions
B. Explosive or Flammable Atmospheres (ATEX Zones)
i. Explosion-Proof Motors and Controls
-
Electric hoists must comply with ATEX or IECEx certifications
-
Non-sparking motors, housed in flameproof (Ex d) enclosures, are essential
-
Pneumatic or hydraulic hoists are often preferred to avoid electric sparks
ii. Static Discharge Prevention
-
Use of anti-static materials for the hand chain and housing
-
Proper grounding systems to dissipate static buildup
-
Surface resistance testing for hoist components
iii. Surface Temperatures
-
All external parts must stay below ignition temperature of the surrounding gas/dust
-
Temperature sensors and thermal cut-offs can prevent overheating
iv. Material Selection
-
Copper-alloy chain guides and bronze hooks prevent sparking on impact
-
Avoidance of ferrous metals where sparks may be generated through abrasion
C. High-Radiation Environments
i. Radiation-Resistant Materials
-
Standard polymers degrade quickly under radiation. Use metal housings and ceramic-insulated wires
-
Lead-lined or tungsten shielding may be required around critical components
ii. Remote Operation Systems
-
Radiation restricts direct human access. Hoists should include:
-
Long-distance pendant controls
-
Robotic interfaces or programmable logic controllers (PLCs)
-
CCTV monitoring for load positioning
-
iii. Redundancy and Safety
-
Fail-safe brakes and double safety latches protect against malfunction
-
Auto shutoff and load detection to prevent overloads under remote control
D. High or Low Temperature Environments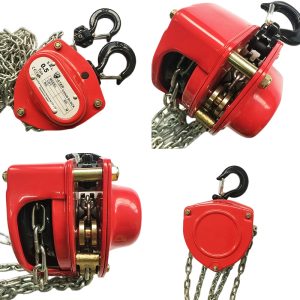
i. Cryogenic Conditions (Below -40°C)
-
Use of specialized chain lubricants that remain fluid at low temperatures
-
Chains made from austenitic stainless steel that resists embrittlement
-
Electrical enclosures with internal heaters to maintain motor functionality
ii. High-Temperature Conditions (Above 200°C)
-
Heat-resistant seals and grease (e.g., molybdenum disulfide-based)
-
Use of heat shields to protect motors and gears
-
Insulated control cables and ceramic-coated components for radiant heat resistance
4. Power System Innovations
Depending on the hazard classification and conditions, different power systems offer unique advantages:
a. Pneumatic Chain Hoists
-
Ideal for explosive or wet environments
-
No electrical components to spark
-
Lightweight and simple to maintain
-
May include stainless steel air motors for underwater use
b. Hydraulic Chain Hoists
-
High lifting capacity
-
Useful underwater and in mining or oil rig settings
-
Can be remotely powered from a secure location
c. Battery and Solar Options
-
In remote locations, battery-powered electric hoists with low-voltage controls improve safety
-
Solar-charged systems reduce the need for flammable fuel stores
5. Safety Enhancements and Monitoring Systems
In extreme environments, continuous monitoring is critical to prevent failure and protect personnel.
a. Integrated Load Cells
-
Real-time weight feedback prevents overloading
-
Helps assess shifting loads in underwater or offshore conditions
b. Auto Shutdown Mechanisms
-
Hoists can be equipped with fail-safes that cut power in case of overheating, jamming, or line tension anomalies
c. Wireless Data Transmission
-
Some advanced systems use IoT connectivity to monitor vibration, temperature, and torque
-
Helps schedule predictive maintenance before a catastrophic failure occurs
6. Case Studies and Real-World Applications
a. Subsea Pipeline Installation – North Sea
An ROV-operated hydraulic chain hoist was used to position pipeline sections 150 meters underwater. The hoist included marine-grade stainless steel construction, waterproof seals, and remote video-assisted controls.
b. Nuclear Waste Facility – Japan
Electric chain hoists with radiation-hardened wiring and robotic interface were installed in a restricted-access nuclear decontamination zone. The system operated via remote control with multi-sensor feedback.
c. Oil Refinery ATEX Zone – Middle East
Explosion-proof pneumatic hoists with bronze wheels and grounding kits were used in Zone 1 classified areas. Operators used extended pendant cables to control the hoist from a safe distance.
7. Design and Compliance Standards
Redesigning hoists for hazardous conditions means adhering to international safety and performance standards:
-
ATEX (Europe) – For equipment used in explosive atmospheres
-
IECEx (Global) – Electrical equipment certification
-
NEMA/IP Ratings – For enclosure water/dust ingress protection
-
DNV & ABS Certifications – For offshore and marine lifting gear
-
ASME B30.16 – Safety standards for hoists
Compliance is critical not only for safety but also for legal operation in regulated industries.
Conclusion
Chain hoists are powerful tools, but their adaptability to hazardous and extreme environments depends on engineering innovation. Whether submerged in saltwater, exposed to flammable gases, subjected to nuclear radiation, or operating in temperature extremes, chain hoists must be purpose-built to ensure safety, reliability, and performance.
Through advanced materials, customized power systems, remote control interfaces, and strict compliance with safety standards, manufacturers can produce hoists capable of thriving in the harshest environments on earth—or under it.
As industries expand their reach into more dangerous and remote areas, the demand for such resilient lifting technology will only grow. The future of chain hoists lies not just in lifting more—but in lifting smarter, safer, and inclusively across all conditions.